Push-Through wheel center cap is an important automotive accessory. It is mainly used to protect the center part of the wheel to prevent dust and dirt from entering and also serves as an aesthetic function. Its production process involves several links; the following is the detailed production process.
I. Design Stage
Market Research
Companies usually conduct market research before producing push-through wheel center caps to understand consumer needs and market trends. This stage involves analyzing competing products and an in-depth understanding of the preferences and needs of target customers.
Product Design
Based on the results of the market research, the designer will carry out the preliminary design of the product. This stage includes selecting materials, determining size and shape, and designing the appearance. Computer-aided design (CAD) software is widely used to create detailed design drawings, ensuring that every detail meets functional and aesthetic requirements.
II. Material Selection
Material Types
Push-through hub center caps are typically made of plastic, aluminum, or stainless steel. Plastics are lightweight and low-cost, while aluminum alloys provide better strength and corrosion resistance. Stainless steel is favored for its durability and aesthetics.
Material Sourcing
Once the materials have been identified, the business will establish contact with suppliers to procure the required raw materials. Ensuring that the quality of the materials meets the standards is crucial, as this directly affects the performance and longevity of the center caps.
III. Production Stage
Molding process
Injection molding: For plastic center caps, the common production process is injection molding. The plastic granules are heated to a molten state and then injected into the mold to form the desired shape after cooling.
Stamping: For metal center caps, the stamping process is commonly used. The metal sheet is put into the press machine and the basic shape of the center cap is formed by the impact of the die.
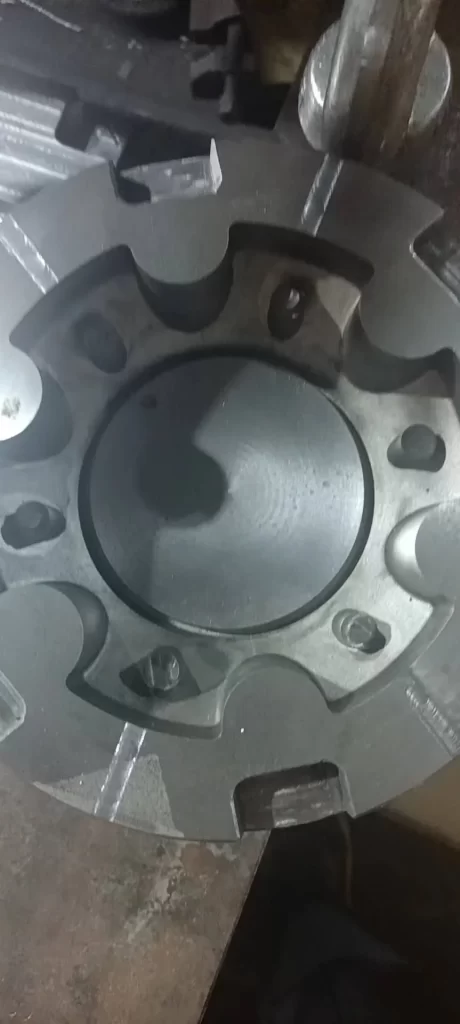
Surface treatment
After forming, the center caps require surface treatment to improve their appearance and durability. Common treatments include painting, anodizing, and plating. These treatments not only add aesthetic appeal but also enhance rust and corrosion resistance.
Logo Printing
Brand logos or other graphics are often printed on the surface of center caps. This process can be done using screen printing or digital printing techniques to ensure that the graphics are clear and long-lasting.
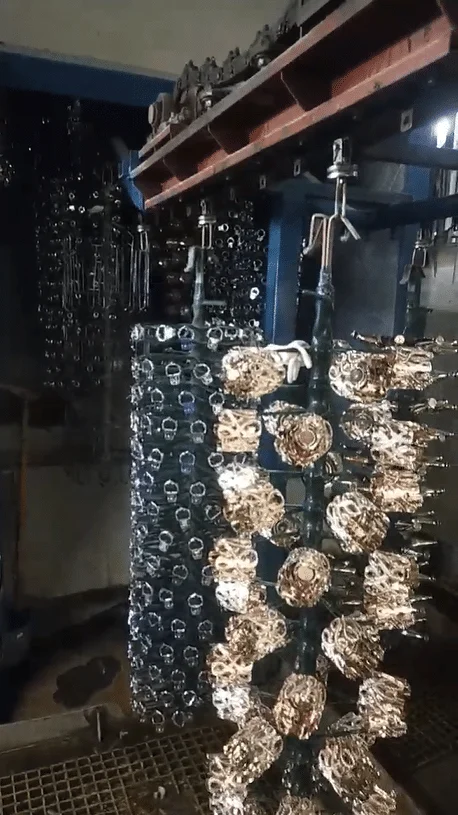
Quality Inspection
Size Inspection
During the production process, each batch of center caps is inspected for size to ensure that it meets the design specifications. This is usually done using calipers or CMMs for accurate measurements.
Performance Testing
Performance tests such as pressure and temperature resistance are performed on center caps to ensure their reliability in actual use. Through these tests, potential problems can be identified and adjusted in time.
V. Assembly and Packaging
Assembly
Although the push-through hub center cap is usually a single component, it may need to be assembled with other parts in some cases. In this case, workers will follow the standard process of assembly to ensure that each part fits perfectly.
Packaging
Qualified products will be cleaned and then packaged. Packaging materials are usually made of environmentally friendly materials to minimize the impact on the environment. The design of the packaging should also take into account the protection during transportation to prevent the product from being damaged during transportation.
VI. Logistics and Sales
Logistics Arrangement
After the product packaging is completed, it will be transported to various sales points or delivered directly to customers through logistics channels. The efficiency of the logistics link directly affects customer satisfaction.
Marketing and Sales
Finally, the push-through center caps will be sold in the auto parts market, online stores, or direct stores of automobile manufacturers. Companies need to use various marketing tools to increase product awareness and sales.
Conclusion
The production process of push-through wheel center caps covers a wide range of stages from design and material selection, to production and quality testing, to packaging and sales. Each step is critical and affects the final quality and market performance of the product. By continuously optimizing the production process, companies can improve efficiency and reduce costs, thus gaining a foothold in the competitive market.